About the conveyor systems installation project
13 kilometres of installed roller conveyor systems installation, 38 lines, thousands of holes drilled in the ceiling, countless installed structures, thousands of hours spent and millions of calories burned.
Eryk was a part of the installation work for one of the largest investments in fulfilment centre in Europe and for one of the most advanced projects in terms of automation. The facility located in the Netherlands had an impressive size reaching 140,000 sqm – as much as approximately 109 Olympic swimming pools. The total warehouse capacity of this centre was 16 million items. This was capital expenditure on an impressive level.
The fulfilment centre was based on goods-to-person technology. This modern order fulfilment method combines automated storage and retrieval, with accurate and ergonomic transport and order picking processes in the shortest possible time.
All of that was possible thanks to the enormous contribution of our Eryk technicians, who performed electrical and mechanical works on conveyor systems installations. At the peak period of the project, the number of technicians reached 50! After 48 weeks of installation works, our teams of mechanics and electricians could proudly say: we’ve made it!
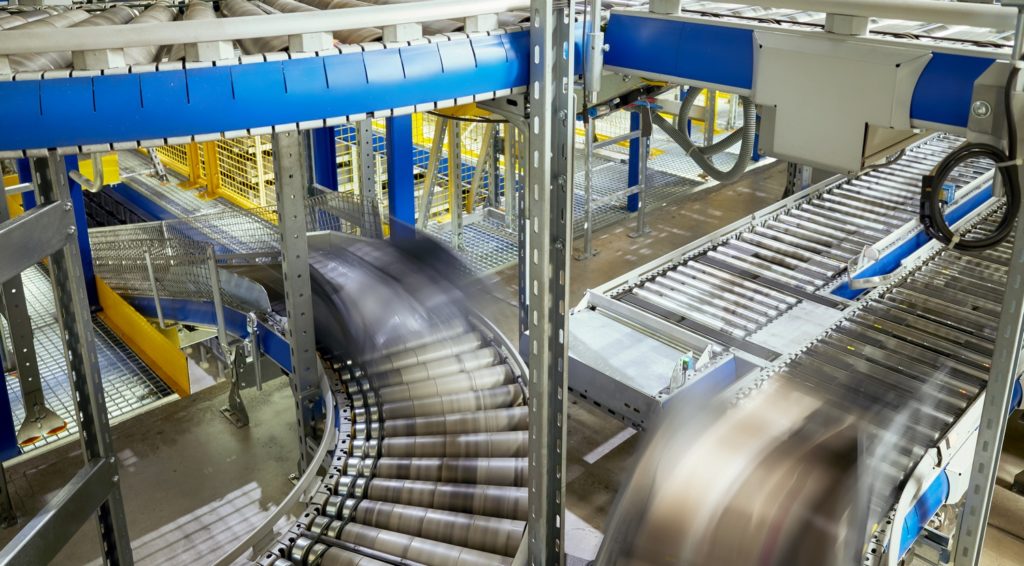
What was challenging in conveyor systems installation on that project?
Michał Charowski, Key Account Engineer, responsible for the project finance & coordination says:
In terms of equipment and technology, there was nothing that could surprise us. The most spectacular were the roller conveyor systems installations in the ceilings – but it was a walk in the park for us ?
(The real challenge was coordinating the work for most of the project, running the works simultaneously on 3 work fronts by 3 teams, when one team was ending and the next was pushing, but we managed. Another big challenge was meeting the deadlines set by the customer, working in unusual spaces and with strange locations of the equipment, often in the corners. Quite often it was dark in many places. In other places we needed to show acrobatic skills.)
Scope of installation works included:
Electrical part:
• Mounting the switch cabinets.
• Mounting the decentral control cabinets.
• Mounting the cable channels and cable tray, covering.
• Cabling and wiring the whole conveyor systems installation.
• Connecting motors.
• Connecting and adjusting optical sensors.
• Profi-net system.
• Labelling
Mechanical part:
• Mechanical assembly of the conveying systems installation.
• Fixing and levelling the conveying systems installation.
• Belt tensioning.
• Installing the railing.
• Installing the whole pneumatic.
• Installing safety devices.
• Belt adjustment.
• Channel adjustment.
Types of conveyor systems installation on this specific project:
- Roller conveyor systems (floor)
- Roller conveyor systems installations in the ceilings
- Transfer belts conveyors.
Types of conveyor systems installations:
There are many types of conveyor systems installations: belt conveyors, roller conveyors, motorized roller, flexchain conveyors, overhead conveyors, mat top conveyors and spiral conveyors. Eryk can provide assembly services of all of them ?
We can categorize them as floor style (mounted on the floor) or overhead conveyor systems installations. They can be used to move products, create buffers and deliver products in sequence for a production line. Read more about projects on eryk.com.